System Architecture Blog Post
Matt Hales and Akshati Vaishnav
May 7th, 2023
Hi! I am Akshati and I am on C2S2's System Architecture sub-team. With the introduction of our new campus partner, the Lab of Ornithology, the system architecture sub-team has recently been involved in determining the system requirements and constraints for this project.
We are working with Christopher Tarango at the Lab of Ornithology who is researching the movement of Scrub Jays and how their movement is associated with the bird's vocalization. In his past work, Tarango has bought tags and has connected an external Pipistrelle (for audio recording) and an external inertial motion recorder to the tag, and has soldered batteries onto the tag; this setup costs him around $1400. Currently, Tarango's batteries last for ~17 hours and the battery's capacity drops drastically over time. Additionally, he needs some sort of waterproofing for the tag to ensure that they are safe from the rain; we do need to ensure, however, that they do not create noise and interfere with the microphone on the tag. There is also a weight constraint associated with this project since, according to the 5% rule, the birds' behavior might be affected if something that is heavier than 5% of their weight is added to their body for long periods of time; this means that the tag on the Scrub Jays should weigh around five grams. We therefore hope to create a bird tag with the goal of improving the length of deployment and reducing birds' stress from tagging.
In order to design this tagging device, we have been determining the system requirements and have been planning/researching potential implementations. For weatherproofing, we have been looking at thermo-contractile sleeves, specifically the non-metallic ones, since we are also looking at wireless communication for easier data transfer (discussed later) and having a metallic covering would result in a Faraday's cage. Additionally, we will be needing a microphone in the tagger to record bird vocalizations. We are thinking of implementing one or both of these two ideas for the microphone: first, we could have a better quality microphone that picks up all noises that the bird makes and encounters; second, C2S2's software sub-team could work on a noise-reduction mechanism that would allow for Tarango to have the noise-reduced data to analyze. We also need an IMU (inertial measurement unit) to get data for the movement of the bird. We would need a power delivery port in order to charge the tags as well as a data port to transfer data. Over the past year, the System Architecture sub-team has also been working on a Caravel chip, which we plan to add to the tag as well. We would have to add flash memory so that we can store data on the tag. We also plan on adding a chip to measure the battery status of the device so that it can communicate with the Caravel chip, and a clock so that we can control when the device gets data. Lastly, there needs to be a mechanical support for the harness so that the tag is easily placed onto the bird. Tarango has been using a rappole-style harness, which allows for the tag to be attached on the back of the bird, similar to a backpack.
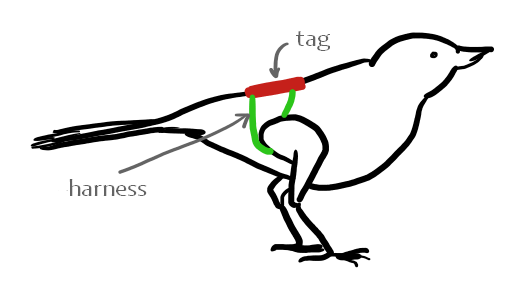
Rappole-Style Harness
Along with the requirements of the system, we have outlined some components that would be nice for Tarango to have. We think that it would be helpful to have a cooling system or choose components that reduce the system from heating up, since the birds are located in Florida and the tags are placed on top of the birds, in direct view of sunlight. Additionally, we think that it would be useful to implement a method of geolocation so that the researchers can find the tags in the case that they are lost. Through talking with Tarango, we realized that charging the tags and collecting data from the tags takes a lot of time. In order to decrease that time, we are thinking of potentially adding solar panels to the tags or implementing wireless charging mechanisms such that multiple tags can be charged at once. For faster data collection, we are looking into potentially installing PIT (passive integrated transponders) tags on the bird tags and antenna near bird nests and/or frequently visited places so that when the birds pass through the area, some data can be transferred to the researchers.
We are currently working on the systems diagram for this device and are still looking to explore more implementations to our requirements. We look forward to working with the Lab of Ornithology and to building something that will be useful for ornithology researchers.
Hi I'm Matt and I'm also a part of C2S2's System Architecture sub-team. This year, the System Architecture team has been tasked with not only understanding the device specifics requested by Christopher Tarango and the Lab of Ornithology, but also developing a shield board for testing our project team's chip after fabrication. The shield board has two main functions: ensuring correct functionality and communication with our chip, as well as creating the framework for interfacing with the peripherals needed for Tarango's bird tags. At the beginning of this semester, we received the fabricated shield board we developed during the fall semester and purchased programmable lab equipment including a power supply (PSU), digital multimeter (DMM), function generator (FG), and oscilloscope. These tools allow us to test for correct input and output voltages, depending on the requirements of each peripheral. An example of this is the use of the Inertial Measurement Unit (IMU) we've chosen. The IMU is important for determining the orientation and movement of the bird thanks to the accelerometer and gyroscope respectively. However, the input voltage of the shield board is 5 Volts whereas the IMU uses an input voltage of 1.8 Volts. Since we aren't trying to fry our IMU, we included two Linear and Low-dropout (LDO) regulators to drop the voltage from the input 5V to 3.3V, and then from 3.3V to 1.8V. When developing any form of technology, you can never just assume it works without testing, so this is where the fun began.
To test our shield board, I got the opportunity to help create a testing library and framework to test everything we wanted to test. The testing library is designed to hold all the necessary functions needed to properly run both the PSU and the DMM. Since these devices require their own specialized inputs, it was a hassle having to consistently perform a 'control + f' to hopefully find the correct commands. DMM.write(':FUNCtion:CURRent:DC') and DMM.query(':MEASure:VOLTage:DC?') are both instances of the types of commands required for setting the input function and the measurement we are trying to record with the DMM. Instead, I created functions that, depending on the user input as a global variable, will instantly affect every instance. As an example, most commands when setting the PSU require the current channel to be assigned, specifically when turning the PSU on, off, or setting the voltage and current: supply.write(':APPL CH1,5,0.2'), where 5 is the input for 5V and 0.2 is for 0.2 A. However, there are multiple instances in the scripts where that would need to be changed. Let's be honest, that creates room for user error and confusion when trying to debug why the script isn't running correctly. By only having to set one variable, this can avoid those errors and allow for more rapid testing with different values. I've also created a way for users to test Voltage versus Voltage, Voltage versus Current, Current versus Voltage, and Current versus Current. But why test Voltage versus Voltage or Current versus Current? This leads back to the LDOs. If we are providing an input voltage of 5V, we need to ensure that the output of the second LDO is actually 1.8V.
There is also one huge benefit with creating the testing library and keeping the main script users run separate: the run script is 10 lines of code, besides comments explaining the inputs whereas the library is over 500 lines of code, making editing a nightmare if the scripts were combined. As of right now, our testing library only contains the functions for the PSU and the DMM, but as our equipment becomes more sophisticated and further testing is required, the team will need to use both the function generator and the oscilloscope, both of which have their own programming requirements and specific commands. While I don't know how much code is needed to run either of these devices, I can only imagine how complex our testing script would become without having the library.
As I am graduating this semester from the Masters of Engineering Program in Electrical and Computer Engineering, it is crucial to me that I do everything I can to ensure that the future of this project team can run smoothly, allowing the next generation of students in the System Architecture team to easily perform any test they want to run, while also allowing students to readily update their testing methodologies. My work this year has been extraordinary and I'm so excited to see what the future holds for C2S2.